Casting
Where Aluminum Transforms into Automotive Masterpieces
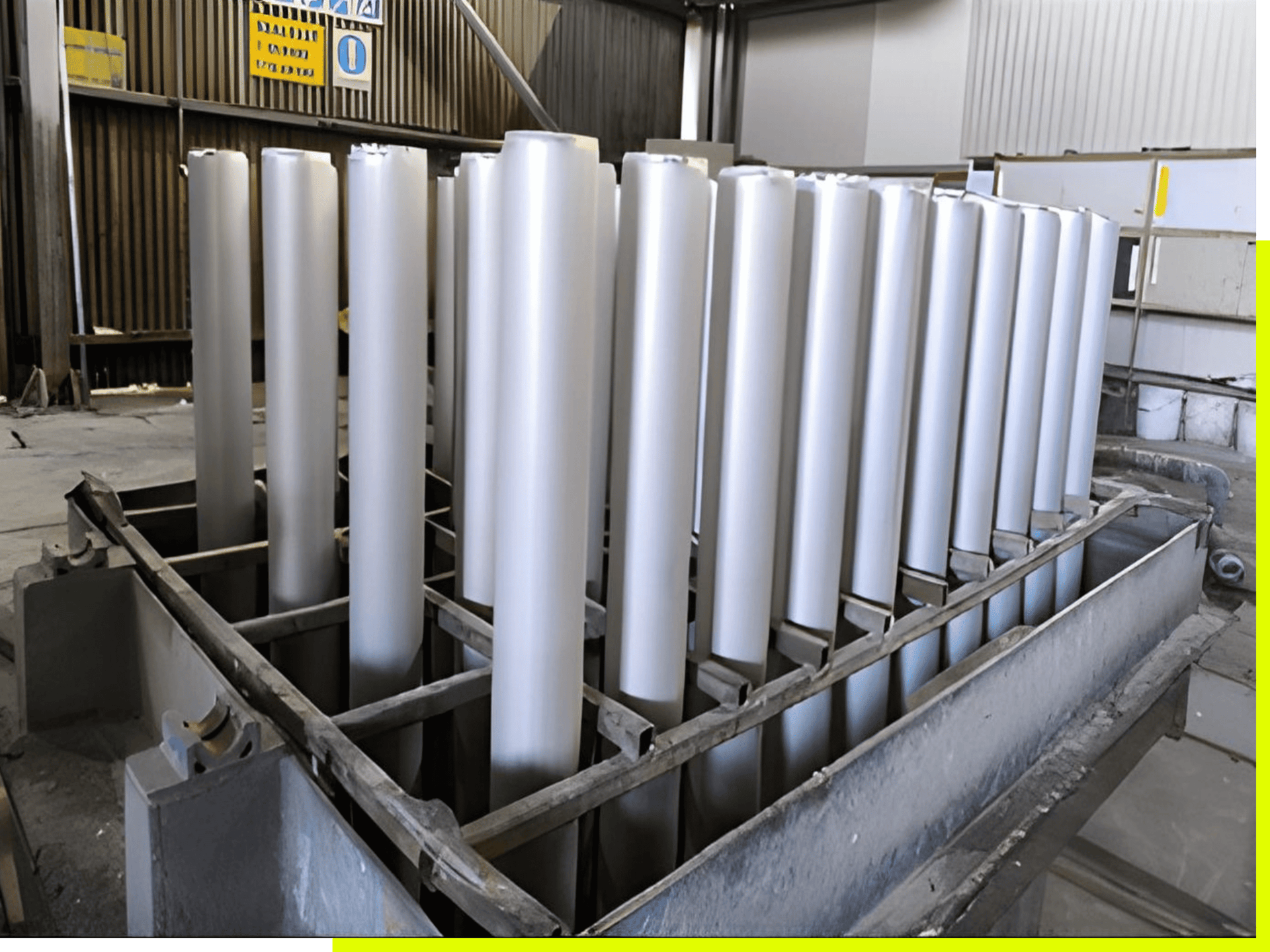
Our foundry achieves extremely high annual production rates, currently using approximately 40-60% recycled materials as well as CO2-neutral primary materials. The foundry’s filtration system employs 400 Aramide sleeves to filter fumes, minimizing gas emissions and promoting environmental sustainability.
At our site in Tirana (Albania), we produce 12,000 tonnes of wrought and cast alloys every year, in the form of cast round billets. We employ the latest technology, including a two-chamber melting furnace, a hearth furnace with an electromagnetic stirrer, and a tiltable rotary furnace. We have the capability to produce all 6000 series alloys and are currently running studies to expand our capability to produce 7000 series alloys.
Another “Tilt Furnace” to be built on 2024-2025.
Supply reliability and quality assurance are very important at Everest.
This not only includes foundry processes but also the recycling of aluminum scrap, as well as the inspection and preparation of the scrap, melting, casting, and homogenization, including fully ultrasonic inspection.
Additionally, a new tilt furnace will be built by the beginning of 2025, with an extra capacity of 24,000 tons per year.
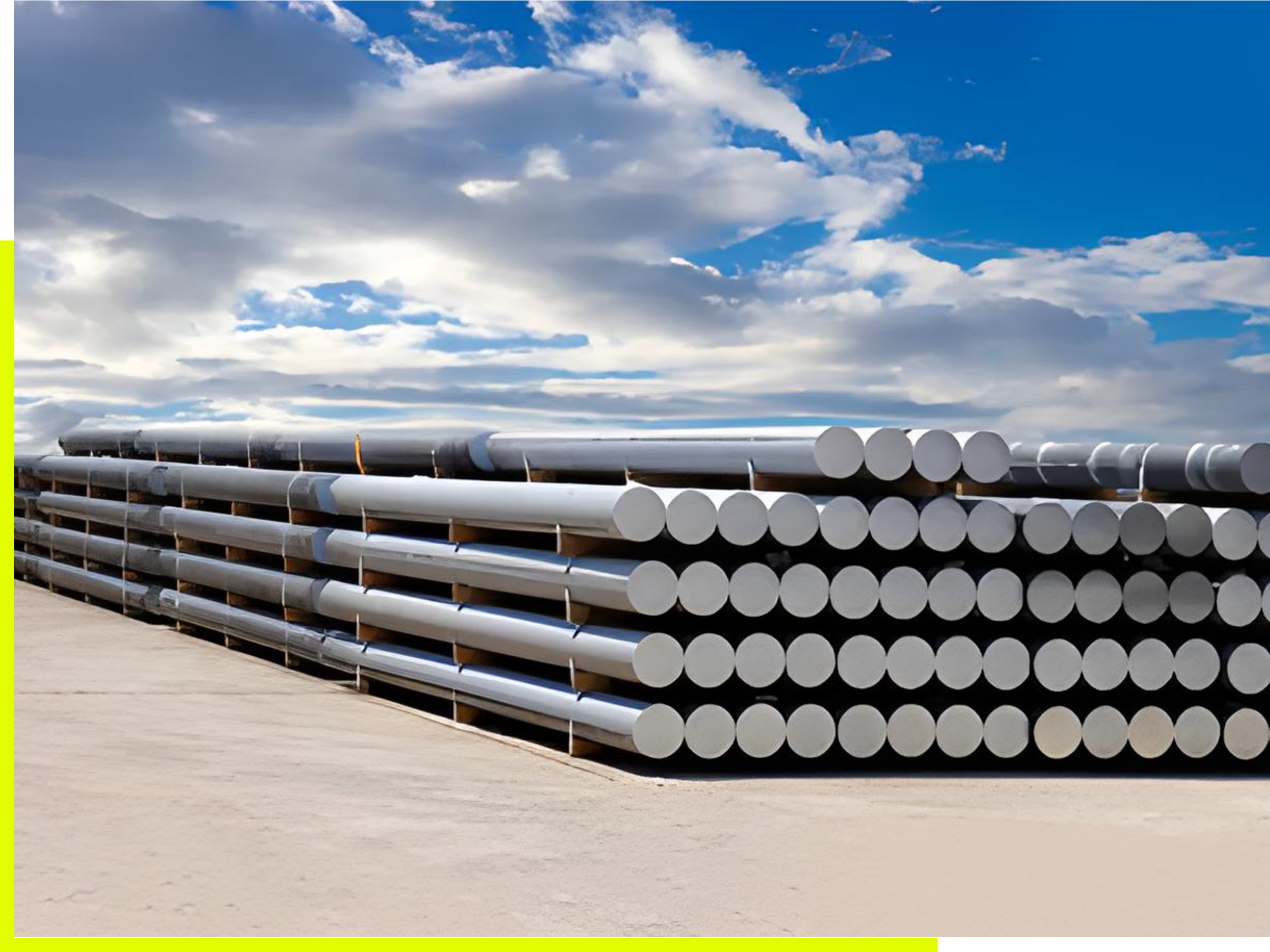